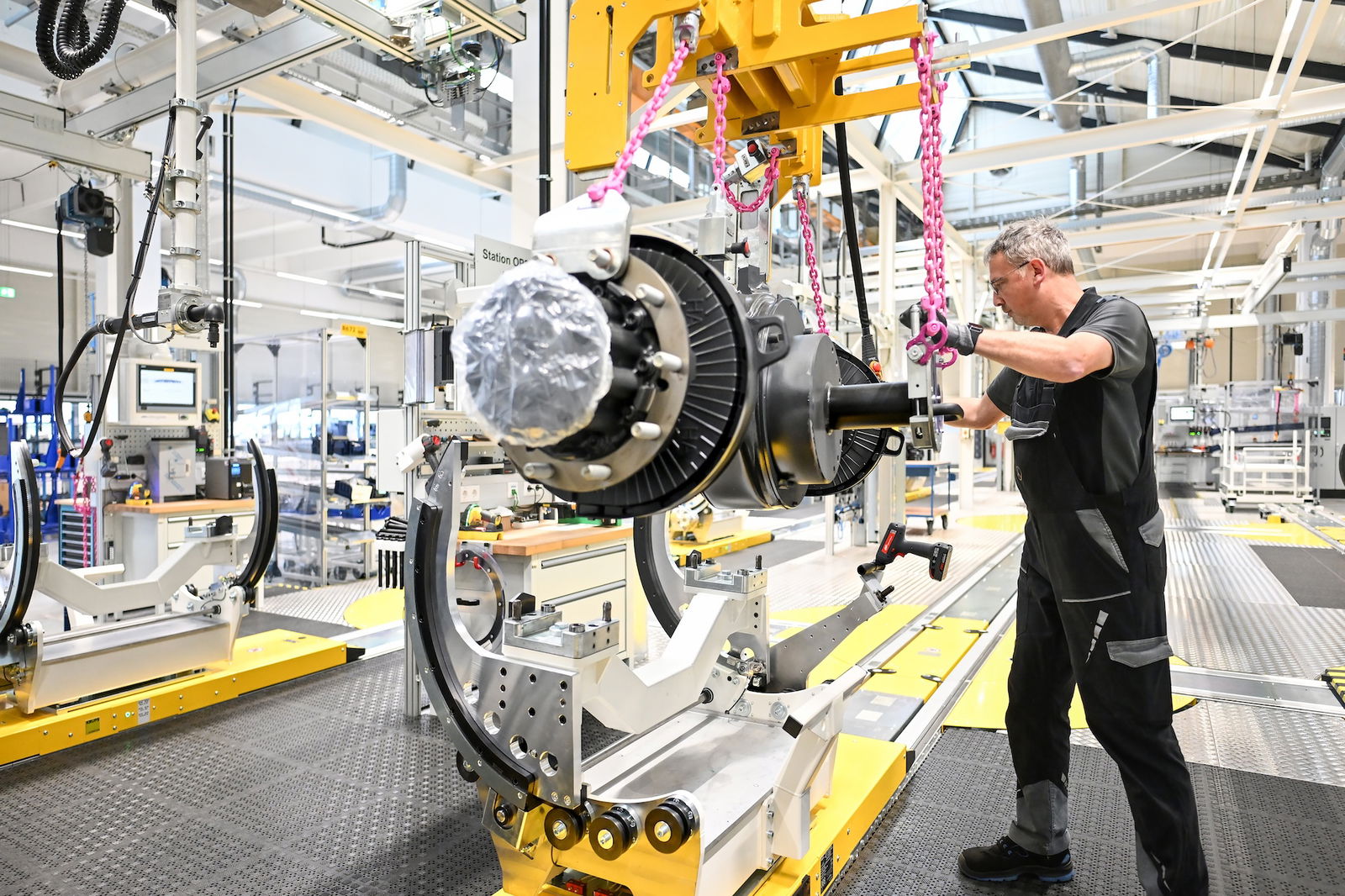
Wie Daimler Truck die E-Achsen für seine Elektro-Lkw baut
- Kommentare deaktiviert für Wie Daimler Truck die E-Achsen für seine Elektro-Lkw baut
- Allgemein
Ende November feiert Daimler Truck im Werk Wörth den Serienstart seines batterie-elektrischen Lkw für den Fernverkehr, des Mercedes-Benz eActros 600, der auf der IAA-Transportation in Hannover als International Truck of the Year 2025 ausgezeichnet wurde. Noch 2024 sollen erste Kundenfahrzeuge gefertigt und zugelassen werden. Zentrale Komponenten des Elektro-Lkw stellt Daimler Truck selbst her, etwa in den Werken Gaggenau und Kassel.
Das Mercedes-Benz Werk Gaggenau, spezialisiert auf schwere Nutzfahrzeuggetriebe, entwickelt sich schon seit einigen Jahren zum Kompetenzzentrum für elektrische Antriebskomponenten weiter. Bereits seit 2021 werden wesentliche Teile für die E-Achse (ein Aggregat, das Achse, Motor und Getriebe vereint und den elektrischen Antriebsstrang darstellt) des E-Lkw eActros 300/400 für den Verteilerverkehr und des eEconic in Gaggenau gefertigt. Dies wird auch für zentrale Komponenten der neuen Generation der E-Achse der Fall sein, die den eActros 600 antreiben wird.
Es handelt sich dabei um mechanische Teile, wie Gaggenau sie bereits seit vielen Jahren für Fahrzeuge mit herkömmlichen Antriebssträngen fertigt. Aus ihnen entsteht das neuartige 4-Gang-Achsgetriebe, das insgesamt rund 30 verschiedene Bauteile enthält. Dazu gehören speziell entwickelte Getriebekomponenten wie Wellen, Zahnräder und Synchronteile sowie Gehäuseteile. Diese Komponenten liefert Gaggenau nach Kassel, wo die komplette Montage der Achs- und Getriebekomponenten stattfindet und somit die neu entwickelte, elektrisch angetriebene Hinterachse entsteht.
Darüber hinaus werden in Gaggenau Komponenten für die Fahrerhauskabine des eActros 600 gefertigt. Zum Umfang gehören dabei unter anderem Rohbaustrukturteile wie Rückwand, Dachrahmen, Stirnwand und Querträger sowie verschiedene Verstärkungen. Es handelt sich dabei um Gleichteile, die bereits beim konventionell angetriebenen Lkw zum Einsatz kommen. Die Rohbaukompetenz des Werkes „trägt“ somit die Außenhaut der neu gestalteten Fahrerhauskabine des neuen batterieelektrischen Fernverkehrs-Elektro-Lkw.
Für alle Elemente des elektrischen Antriebsstrangs bestehen hohe Anforderungen an Qualität, Lebensdauer und Bauraum, wie Daimler Truck in einer aktuellen Mitteilung hervorhebt. So lassen die geometrischen Vorgaben für Oberflächen und Rauheiten der Verzahnungen von Zahnrädern und Wellen beispielsweise nur sehr enge Toleranzen zu. Durch neueste und hochgenaue Fertigungstechnologien, wie zum Beispiel spezialisierte Verzahnungsschleifmaschinen, gelinge es, die geforderte Qualität zu gewährleisten.
Die mechanische Bearbeitung der Gehäuseteile findet im Werk Gaggenau in einer eigens dafür umgerüsteten Halle statt. Hier wurde eine neue Fertigungsanlage mit automatisierten Bearbeitungszentren errichtet. Bereits während der Beschaffungsphase konnte durch die virtuelle Inbetriebnahme dieser Anlagen die Bearbeitung an sogenannten digitalen Zwillingen simuliert werden. Durch dieses Verfahren ergebe sich eine enorme Zeitersparnis im Vergleich zu einem konventionellen Einrichtungsprozess von Fertigungsanlagen. Im Rahmen der mechanischen Bearbeitung wird unter anderem gebohrt und gefräst und es werden Gewinde geschnitten, bevor die Gehäuse anschließend eine Dichtheitsprüfung durchlaufen.
„Im Mercedes-Benz Werk Gaggenau gehen Tradition und Transformation Hand in Hand. Wir sind stolz darauf, unsere jahrzehntelange Erfahrung in der Herstellung hochpräziser Getriebekomponenten in den neuen elektrischen Antriebsstrang einzubringen. Gemeinsam mit unseren Kollegen am Montagestandort Kassel leistet unser Werk einen wichtigen Beitrag zur emissionsfreien Mobilität“, sagt Thomas Twork, Standortverantwortlicher Mercedes-Benz Werk Gaggenau.
In Kassel entsteht die neu entwickelte E-Achse
Das Mercedes-Benz Werk Kassel, das globale Kompetenzzentrum für konventionelle Achsen und elektrische Antriebssysteme, montiert die neue Generation der E-Achse des eActros 600. Die elektrisch angetriebene Hinterachse ist speziell für den Einsatz im Langstreckenverkehr neu konzipiert worden. Sie verfügt über eine Reihe technischer Neuerungen für höhere Leistung und Effizienz.
Die Rumpfachse wird auf das Transportsystem der Endmontage gelegt / Daimler Truck
Im Werk entstand dazu eine neue Montagelinie inklusive Test- und Prüfstationen der funktions- und sicherheitsrelevanten Merkmale. Genau wie für die E-Achse, die aktuell im eActros 300/400 und eEconic zum Einsatz kommt und die bereits in Kassel gefertigt wird, gilt auch für die neue Generation das Gleichteile-Prinzip. Das bedeutet, dass Rumpfachse sowie Radkopf und Bremsenumfänge aus der konventionellen Achse stammen, die das Werk Kassel seit Jahrzehnten fertigt. Diese Komponenten werden flexibel auf der Montagelinie montiert, sodass das Werk je nach Auftragslage zwischen konventioneller und elektrischer Achse variieren kann.
Montageprozess der neuen Generation der E-Achse in Kassel
Der Montageprozess verläuft im Werk Kassel in verschiedenen aufeinander abgestimmten Phasen. Basis für die neue E-Achse bildet die Achsbrücke, die im ersten Schritt für das Tragen, Rollen und Bremsen vorbereitet wird – d.h. hier werden Radnaben, Antriebswellen und Bremsenumfänge montiert. Die Achsbrücke für die E-Achse entspricht der konventionellen Baureihe, so dass sie problemlos an das vorhandene Fahrzeugchassis angepasst werden kann.
Im Montagebereich der elektrischen Antriebseinheit werden die vormontierten Getriebeteile, die beiden Elektromotoren sowie weitere Komponenten in das Achsträgergehäuse, das aus Gaggenau stammt, montiert. In der Endmontage findet die sogenannte Hochzeit zwischen der zuvor entstandenen elektrischen Antriebseinheit und der Achsbrücke statt. Weiterhin werden diverse Sensoren, Öl- und Kühlleitungen sowie Niedervolt-Leitungssätze stromfrei montiert.
Die Hochvoltkabel der elektrischen Hinterachse werden an der Achse und Adapterplatte montiert / Daimler Truck
Bevor die E-Achse das Mercedes-Benz Werk Kassel verlässt, wird sie in der letzten Phase einer detaillierten Funktionsprüfung der mechanischen und elektrischen Komponenten, der sogenannten „End-of-Line Prüfung“ (EOL-Prüfung), unterzogen. Hier erfolgen die Hochvolt-Kabelmontage, die Dichtheitsprüfung und die Hochvolt-Tests. Abschließend durchläuft die E-Achse eine Simulation verschiedener Fahrsituationen inklusive Last-, Topografie- und Gangwahlprofilen. Nach dem Durchlauf der EOL-Prüfung wird die E-Achse für den Transport in das Mercedes-Benz Werk Wörth vorbereitet.
Hauke Schuler, Standortverantwortlicher Mercedes-Benz Werk Kassel: „Wir sind stolz darauf, nun auch eine E-Achse für den CO2-neutralen Langstreckenverkehr im Produktportfolio zu haben. Sie trägt mit ihrem effizienten Design, das den elektrischen Antrieb in das bestehende Achskonzept integriert, zur großen Reichweite des eActros 600 bei. Dies ist ein weiterer wichtiger Meilenstein für das Mercedes-Benz Werk Kassel in der Transformation zur emissionsfreien Mobilität.“
Quelle: Daimler Truck – Pressemitteilung vom 11.11.2024
Der Beitrag Wie Daimler Truck die E-Achsen für seine Elektro-Lkw baut erschien zuerst auf Elektroauto-News.net.